ワンオフパーツ作品集
SRヘッド燃焼室加工
SRヘッド燃焼室加工
SRエンジンのシリンダーヘッド燃焼室の加工(試作品1号)が出来上がりました。
通常、高圧縮化を施す場合、ハイコンプピストン(ピストンの頭の部分を盛り上げた物)を使用したり、ヘッド面を均一に削って燃焼室容積を小さくします(俗にいう面研です)。高圧縮化を進めていくと異常燃焼(燃焼の伝播に関係ない自然着火)が起き始めます。異常燃焼は燃焼室の端の部分から始まります。(燃焼の広がりの最も遠い所であり、ピストンとシリンダーヘッドの空間の最も狭い所ですので)。また、燃焼ガスの力をピストンの上面で受け下に押し下げられることでエンジンは力を発生させますが、そのピストン頭部の形状は当然平らなもの(フラットヘッドピストン)が最も効率が高くなり、複雑な形に盛り上げたものは効率は落ちてしまいます。
そこで考え出されたのが、スキッシュエリアを持つ燃焼室形状です。主にバルブの無いエリアをせり出させた形状で、ピストンが上昇してくると、このせり出した部分との間の混合気が先に圧縮され、その隙間が中心部に対してテーパー状に広がっている為、中心部に向かって吹きだしていきます。結果、最も燃え広がりにくい外端部には混合気が無くなり異常燃焼を起こし難くなります。その上、中心付近はより圧縮が高まり高い燃焼効率が得られるようになります。また、シリンダーヘッド側で容積を小さくするので、ピストンヘッドはフラットに近いものが使えるようになります。
70年代終盤に広まってきた理論で、あまりパワーや燃焼効率を求めないSRの場合、圧縮も低いので最も一般的な半球状の燃焼室でした。圧縮を上げるなら、これを試してみたいと考えていました。TIG溶接でアルミを盛った後、削って、形状と容積を整えます。実験ですので出来るだけ圧縮比が高くなるようにしてみました。500クランク・400ピストンとの組み合わせで、圧縮比が約12.0:1になります。(本来は完全なフラットヘッドの500ピストンにしたかったのですが、あまり圧縮が高くならなかったので400ピストンにしました) これまでのヘッドとの比較をしやすいように、ポート研磨もしています。
さすがに少し圧縮が高すぎて、点火時期や進角特性を変更しなければならないかもしれませんが、まずは純正のイグニッションシステムで試してみようと思っています。出来上がりが遅くなってしまったので、2016シーズンに向けて冬季の間に組み替えて春にテストする予定です。
ちなみに、ワンオフなのはこの作業(溶接)をする為の冶具の方です。シリンダーヘッドの歪むのを防ぐように、頑強な板材で上下をサンドイッチし、出来るだけ歪み難い方法で溶接していきます。結果、歪みは問題ありませんでした。今回は冶具の製作をしやすいようにアルミ2017材・20mm厚の板材を使ってみました。
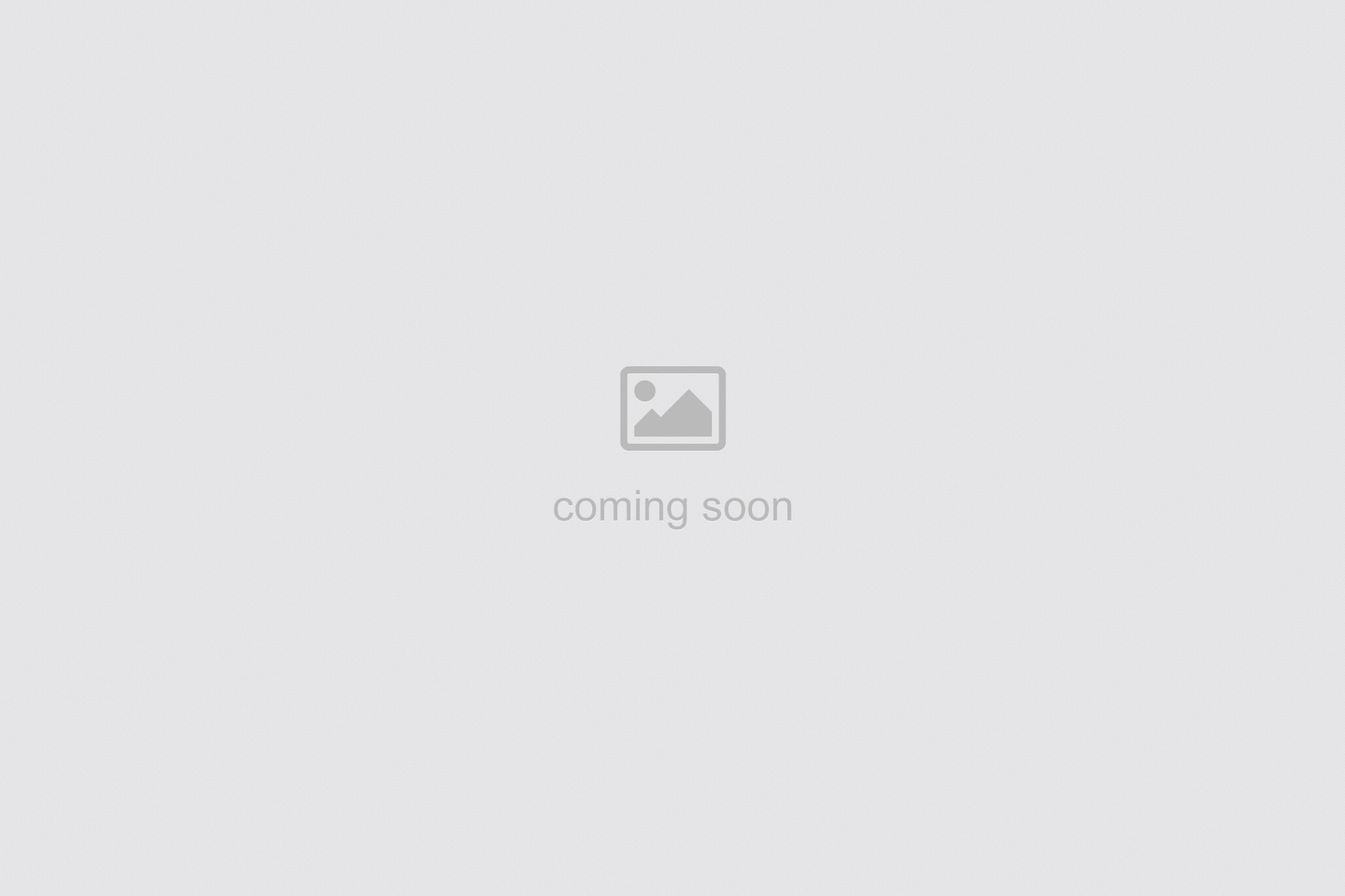