カスタマイズについて
カスタマイズ事例
カスタマイズ テスト報告
パドックⅢ カスタマイズ計画 ブログ
2023東京モーターサイクルショー観てきました
2023-04-05
去る3月24日に、当店の加盟している「AJ(全国オートバイ協同組合連合会)」が後援・出展している関係で、会議出張を兼ねて、「東京モーターサイクルショー」に行くことが出来ました。コロナ渦で中止されていた後、昨年は各種イベントの無い展示のみで開催されていたものの、今年はコロナ前を上回る規模で開催されることになっていたので、期待していました。
前週には大阪でも開催されていたので、今年のモーターサイクルショーは直接観た方も多いとは思います。モーターショーと違い世界初公開 の新型車(今回はカワサキ・エリミネーター400のみ)などのセンセーショナルな話題は少ないものの、アフターパーツメーカーの出展が多数あり、カスタマイズ好きの方には見所の多いショーとなっています。
初日午前中の特別公開を観ることが出来たので、時間に限りがあって駆け足ながら、それほどは混雑のない状態で観て回ることが出来ました。
近年のネオクラシック系の人気はさらに高まっているようで、バイクメーカーの新型車両をはじめ、アフターパーツメーカーにとっても「ネオクラシック」をいかに仕上げるかのアピールが多かったように感じました。※個人的な感想です
ネオクラシック系も、昔のオーソドックスなスタイルやカフェレーサー風スタイルから、現代的ながらもバイクらしさを表現したスタイルまでバリエーションが増えて、各社とも力が入っていて頼もしく感じ、これからもバイクの魅力を追求してもらいたいと思いました。
当店にとっても、カスタマイズの参考になるショーでした。
※個人的には、新型XSR900ベースのY’sギヤ製外装のデザインが秀逸で気になりました。フレームをはじめとした車体とエンジン、そして外装がうまくマッチしていて、これにどんなカスタマイズを加えると良いか想像していました。
※直接会場には行くことが出来なかった方も、各メディアなどで、ぜひご覧ください。
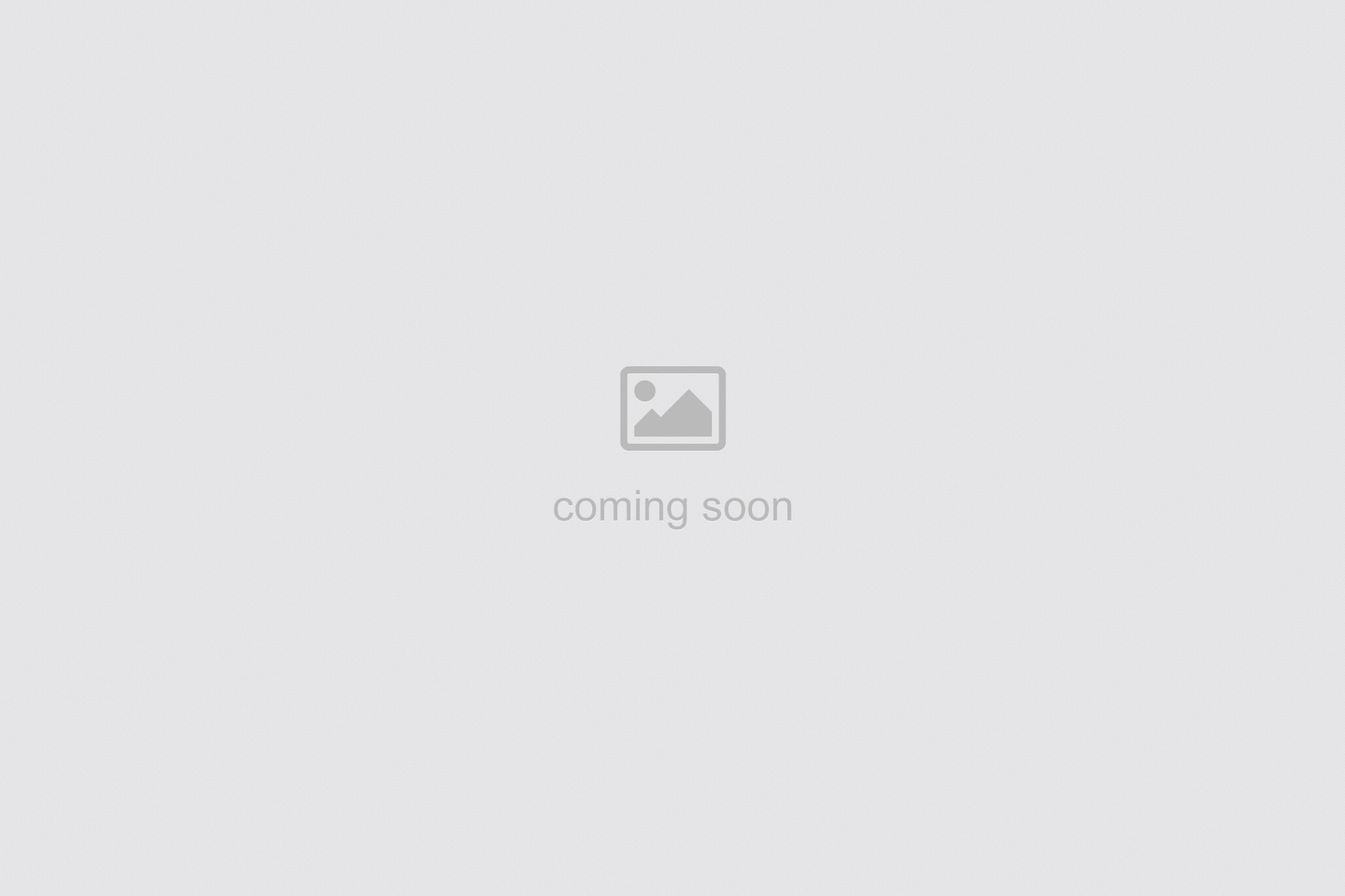
フレーム修正機・導入
2023-03-13
この度、唐突な成り行きで「フレーム修正機」(中古品=もちろん2輪車専用)を導入しました。
これまで、フレーム修正を依頼してきたショップさんとは長年のお付き合いで、一般的(修理)な修正をはじめ、オリジナルフレーム製作やフレーム補強を施す際には、お世話になっていました。
年明けに1台の依頼をしたところ、近年は需要(フレーム修正の)も減ってきて、あまり携わることが無くなっていたことと、高齢化(私自身もそこそこ高齢ですが、かなり体力が必要とのこと)のため、修正機を譲るから自分でやらないか?との提案を受けました。当店においても、修理としてのフレーム修正となると本当に久しぶりなくらいですが、フレーム補強や製作の際の「修正」は、アライメントの精度を出すための「必須となる工程」ですので、自分でやるしかないと譲り受けることにしました。
安価に譲っていただいたものの、当方では搬送(背の低いユニックが必要)してもらえる業者さんがなかなか見つからずにいましたが、そのショップさんに心当たりを紹介してもらい、搬送することが出来ました。かなりの大きさ・重量なので、整備工場内にはとても設置することは出来ないため、車庫(建築基準は倉庫兼工場)の中に設置しました。修正作業時では、車体前方からの作業が主体となるため、奥に向かってバックで乗せられる位置(中2階の下)に設置しましたが、これが後に良い結果となりました。
長く使っていなかった修正機は、かなり汚れていて、すぐには作業の出来る状態ではなかったため、まずは「治具の確認」を含めて清掃・洗浄からはじめました。そのショップさんで作業を見たことはあったものの、使用方法の分からない治具も多く、実際の作業で試していくしか無さそうでした。
作業に取り掛かると、第一段階の車体を修正機に「固定」することから、問題が発生しました。車体の固定は、フレームの基準である「スイングアームピボット部」に固定用治具(支柱に連結)を差し込み、土台の「中心線上」にセットします。車体下からジャッキで後輪側を持ち上げて、ピボットシャフト(車種によりスイングアームごと外して)を抜き、治具を差し込まなければならないのですが、わずかなズレでも簡単には入りませんでした。強引に叩き込めば入らなくはなさそう(実際にかなり叩いた痕跡あり)でしたが、今後(今回の車両は軽量級)を見据えて、何か他の方法を考えることにしました。
車体を下から支えた状態では、わずかでも動かすのは難しい(危険も含めて)ことから、上から「吊り下げる」のが良いのではないかと考えました。ここで設置場所の利点が出ました。ちょうど中二階(鉄骨製)の下になるため、鉄骨を利用して「チェーンブロック」を設置することが出来ました。※チェーンブロック(手動)は4輪車のエンジン吊り上げ作業などではポピュラーで、昇降の微調整がしやすい道具です。鉄骨が無かったら「門柱=これもエンジン吊りには必須」が必要になるところでした。
これで再挑戦したところ、「簡単」に治具も差し込めて車体を固定することが出来ました。あとは、試行錯誤しながらも、なんとか修正作業を進めました。今回の車両では、溶接部付近のクラック(割れ)もあって、溶接作業(200Vの溶接機で整備工場内にしか引いてない)のために1度修正機から移動(前後足回りをいったん仮組)して溶接、そののちに再度修正機にセットして、最終確認(溶接歪みの可能性)する必要がありました。
初めて自分で行った「フレーム修正」でしたが、なんとか完遂することが出来ました。不慣れなため、治具の当て痕を残したミスをしてしまいましたが、アライメントとして最も重要な「ヘッドパイプの垂直※1」は、しっかりと出せた仕上がりになりました。
組立後の試運転でも、見事な「直進性」と左右で違和感のない「旋回性」を確認出来て、安心しました。
治具の扱いや修正時の力の掛け方など、まだまだ技術不足ですが、工夫をしながら研鑽していきたいと思っています。
※1 「ヘッドパイプの垂直」とは、地面と平行なピボット部(後輪が直立)に対して、ヘッドパイプ軸が完全な垂直(進行方向から見て)になることで、「前輪を直立」にすることです。ヘッドパイプ軸がわずかでも傾いた状態では、直進しようとする後輪(車体)に対して、前輪は旋回しようとしてしまい、まともに直進出来なくなるだけでなく、コーナリング時でも前輪と後輪が違う旋回半径を描こうとして無理な力がかかり、スムーズな旋回が出来なくなります。そのため、アライメントの中でも最も重要視しています。
オリジナルフレーム製作時はもちろんのこと、「フレーム補強」においても、元の状態がすでに曲がっているようでは、補強を施しても[良いフレーム]にはならないので、ヘッドパイプ軸の「チェック」と「修正=必要に応じて」は、欠かせない工程になります。
※2 バイクのフレームは常に大きな力を受け止めているため、どんな車両でも僅かな「歪み」は起こっている可能性はあり、「アライメント点検・フレーム修正」は、個人的には「メンテナンス」の一環と考えてはいます。とは言え一般的には「フレーム修正」を施した車両は、「修復歴車」に当たりますので、再販価値(中古車としての)が下がってしまうため、一般の人にはおすすめ出来ないのが実情です。
そのため、当店では「カスタマイズ」として捉えて、「より良いバイク作り」のメニューのひとつとして「おすすめ」したいと思います。
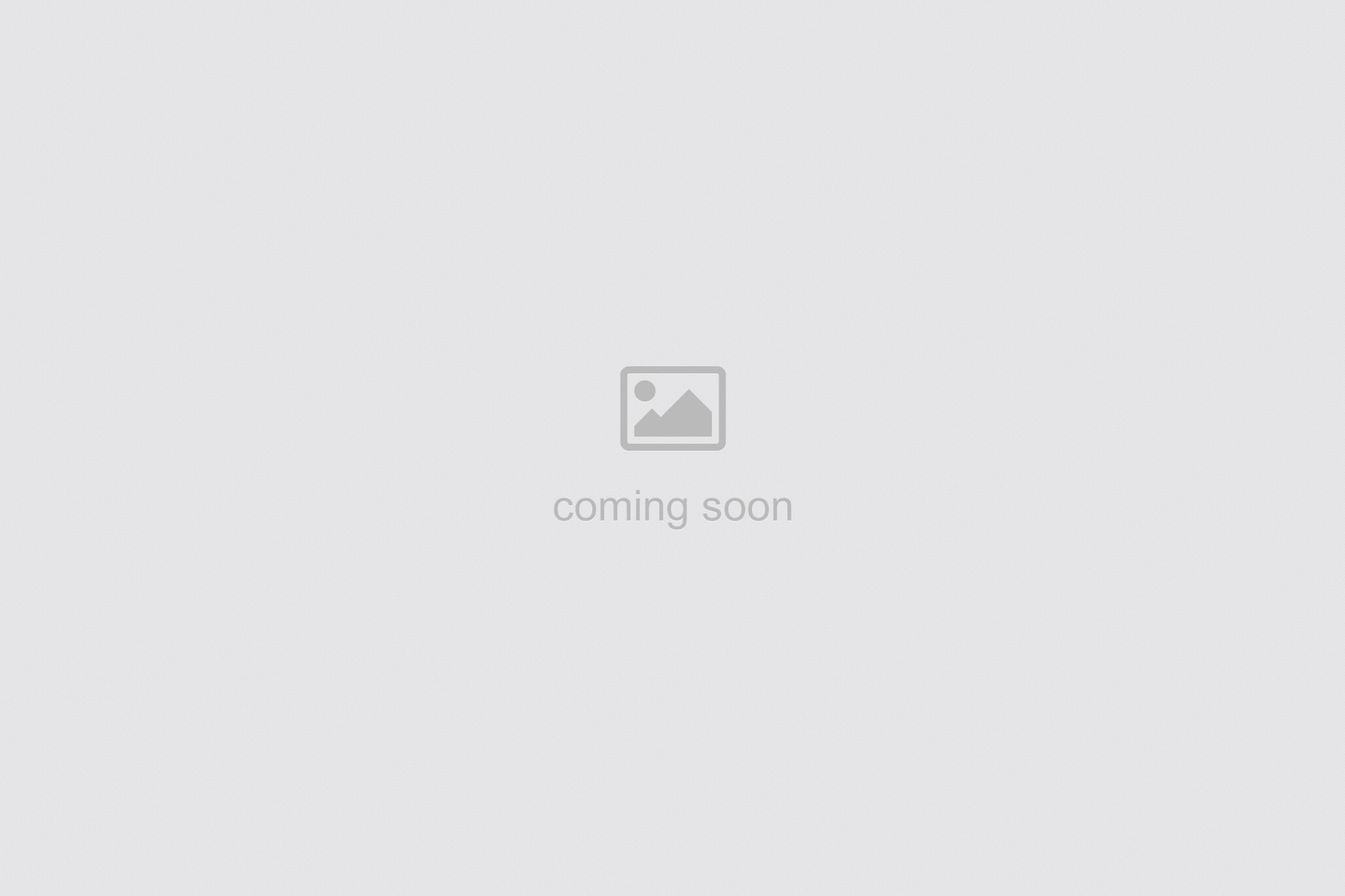
キックペダルラバー装着&車検・SR
2023-02-25
ステップ周りの作業を終えた直後に、車検を控えていたこともあり、思いついて「キックペダルラバー」の装着にチャレンジすることにしました。
現状(社外品)のキックペダル本体はラバー非装着(むき出しの鉄棒)のため、「ケッチン」の衝撃は相当のもので、これまではエンジン始動時にはその都度「レーシングブーツ」に履き替えていました。テスト始動のたびに履き替えるのは面倒に感じていて、なんとか衝撃をやわらげることが出来ないか?と思っていました。
当然のこと適合する物は有りませんが、SRの純正品がかなり太くて厚みがある物なので、内側を削ればいけるかもしれないと、試みてみることにしました。実際に計測すると、SRの純正ラバーの内径は約10mmで、太さ14mm径(両端を除く主要部分)のペダルバーがはめられるようになるまで、ドリルで広げることにしました。
手持ちのドリル刃では12.5mmが最大だったので、とりあえずこれを用いて始めてみました。ゴム製品は一般になかなか削ることが難しい材質ですが、わりと硬目のゴム材であったことから、何とか孔を広げる(何度も繰り返し通して)ことが出来ました。それでもまだ細目の孔にしかなっていませんでしたが、ヒーターで温めながら挿入したところ、かなりの無理やりとは言え装着することに成功しました。
見た目が純正のよう(少し野暮ったい)になってしまいましたが、実際にずいぶんと衝撃は緩和(何度かケッチンが起こって実証)されて、普通のシューズでも安心してキック出来るようになってくれました。
ステップ周りのおまけのような些細なことでしたが、その効果のほどに、もっと早くにしておけば良かったと思わされました。
※参考
「ナノタイプウィンカー」をはじめ「フルLED」となってから、初めての車検(陸運支局への持込検査)でしたが、灯火類をはじめ問題無く合格しました。最初に担当してくれた検査官が2輪に不慣れだったようで、戸惑いもあったものの、後に詳しい検査官に代わってしっかりと保安基準(ウィンカーのEマーク・取付寸法)の確認をしてくれました。
Eマークの目視による確認はもちろんのこと、左右の間隔では実際にメジャーで計測されました。特にフロントウィンカーは、本体の張り出しが小さく、左右間隔(レンズ内縁)も見た目には狭く(少しは余裕を持たせてあるのですが)感じるようで、実測するのは仕方がないでしょう。
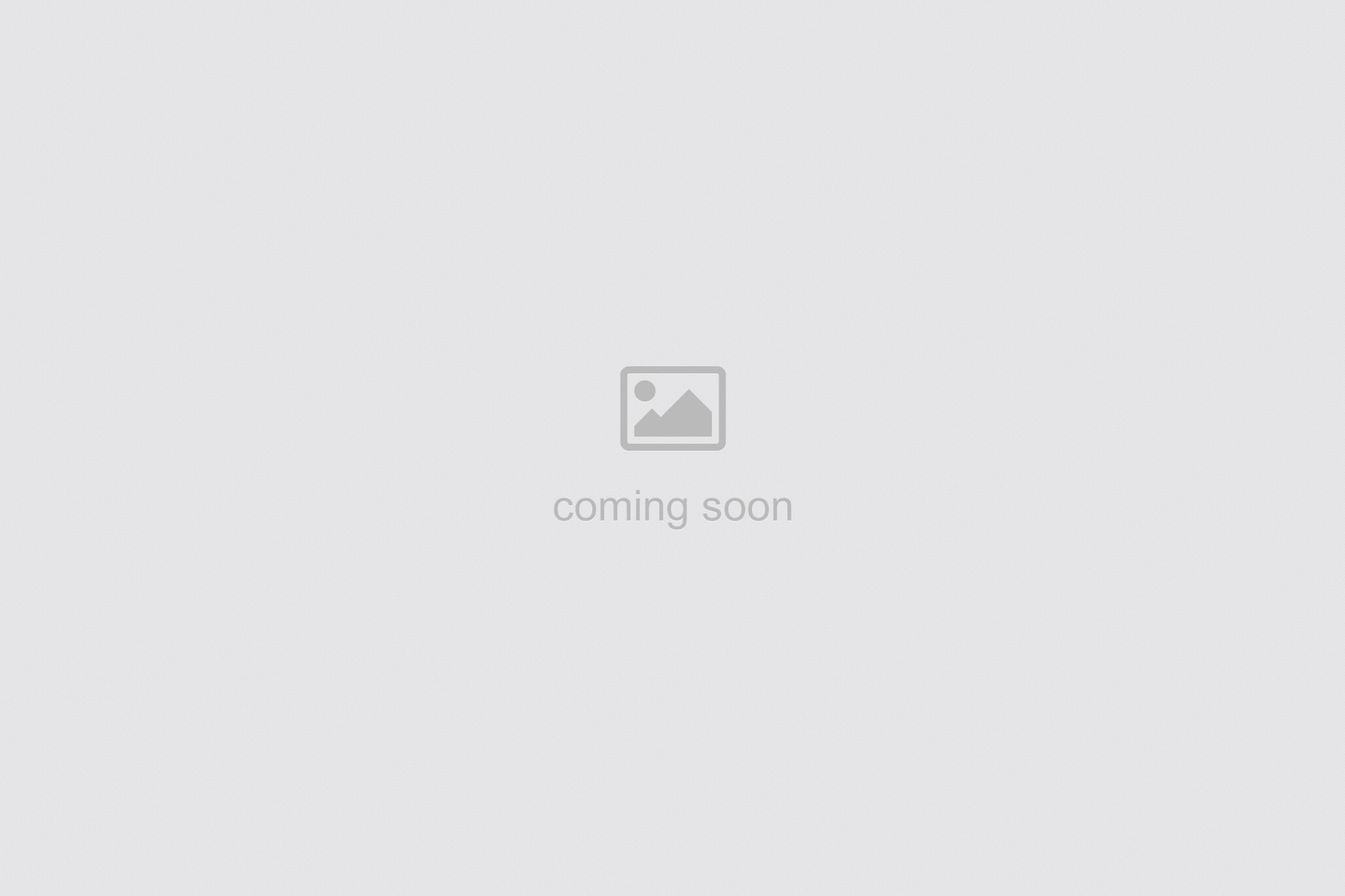
リヤマスターシリンダー換装&ステップ位置変更・SR
2023-02-18
昨年、ブレンボ製フロントマスターシリンダー(RC390・隼など)のオーダーを受け、卸販社さんのサイトで調べていて目についたのが「リザーバータンク一体型リヤマスターシリンダー」でした。タンクホースなどを無くして、シリンダー本体とリザーバータンクを鋳造で一体成形した製品です。これなら、ステップ周りがスッキリとしそうで、面白そうだと思いました。
リーズナブルな価格(国産車の純正部品より安い位)や、キャスティング(鋳造)製であることを考えると、おそらくOEM(メーカー不明)品だと思われます。シリンダー径13mmで、わりと互換性(純正品には1/2インチや12mm径が多い)が高いので、使える車種も多かろうと仕入れて展示していました。
サイズとしては互換性は高いものの、一番の特徴である「一体型タンク」では、タンク(マスターシリンダー)が直立に近く設置されなければならないため、ステップ周りのレイアウトはかなり限定されます。※一般的にスーパースポーツ系は前倒し・ネイキッド系は後倒しのレイアウト(フレーム形状による)です。よく考えると、意外と装着可能なバイクは、多くは無さそうでした。
それならと、しばらく展示した後に、当店のSR(現状ZXR400純正1/2インチ)への装着を試してみることにしていました。SRは多くのネイキッド系と同様に、アンダーフレームがリヤショックアブソーバー取付部へと続くフレームですので、マスターシリンダーを直立させるとフレームに被る位置になります。ただ、狭目のピボット幅なので、何とか出来そうだとは考えていました。作業はシーズンオフになる頃を予定していました。
そうしていたところ、別の点でもステップに関して仕様変更の必要性が出てきました。2022シーズンの終わり直前に、リヤショックアブソーバー(ナイトロン製)の換装をして走行(結局1回きりでしたが)したところ、それまでより荷重をしっかりと掛けることが、出来るようになっていました。より積極的な体重移動も可能になった結果、ステップ位置を少し変えてみたくなりました。
そこで、ステップ位置の変更をしつつ「ブレンボ製リヤマスターシリンダー」の装着出来る「ステップセット」(ステッププレート&マスターシリンダーブラケット+プッシュロッド)を製作することにしました。
ステップバーの位置変更は、約1cm高く設定し直しました。もう少しとは思いましたが、とりあえず足が離れないようになれば良いので、あまり一般走行で、膝がきつくなり過ぎないようにしました。
ブレンボ製リヤマスターシリンダーの設置に当たっては、当初のイメージでは、リザーバータンク側が後に背負うようにレイアウトすることを考えていました。ところが、そうするとブレーキホース取付部(シリンダー本体側頭頂部)がタンクより下がった位置になり、ブレーキホースの取り廻しがタンクを迂回するように接続しなければならなくなってしまいます。違和感は有りましたが、前後を逆にしてタンクがフロント側になるように設定し直しました。
プレート・ブラケット以外に、プッシュロッドを製作しました。国産車のリヤマスターシリンダーのほとんどが、プッシュロッドごとピストンストッパー(サークリップ)でシリンダー側に装着しているのに対して、「ブレンボ製」はプッシュロッドは含まれない構造(おそらくOEM品として汎用性を上げているのだと思われます。)になっています。プッシュロッドは、ペダル側にのみ連結されることになります。ロッドはピストンを押す棒状(調整用のネジは必要)であれば良いので、構造はそれほど複雑なものではありません。ブレーキペダルとの連結にピロポール(M6メス)を使うのは変わらないため、通常のM6ボルト(ステンレス製)の頭を削り落として丸く仕上げて出来上がりです。
プッシュロッドがマスターシリンダーに固定されないため、ペダルが持ち上げられると、そのままロッドが飛び出てしまうので、ペダル上側にストッパーを設ける必要があります。丸棒材を切り出したカラーですが、中心をずらして偏心させたボルト穴にして、ペダル高さを調整可能にします。
リヤマスターシリンダーの変更によっての性能への影響は、ほとんどありません(フィーリングに少し変化があるはずですが、足の感覚では感じ取れるほどではないでしょう)が、あまり見慣れないルックスにはなって、良い感じに仕上がった(個人的に)と思います。
懸念していた「フレームと被るマスターシリンダー」のレイアウトによる影響ですが、ステップバー&ブレーキペダルを、前仕様より5mm外方向に出すだけで干渉を避けることが出来ました。キックペダルの踏み込みやライディングにも、問題無く使えるように出来上がりました。
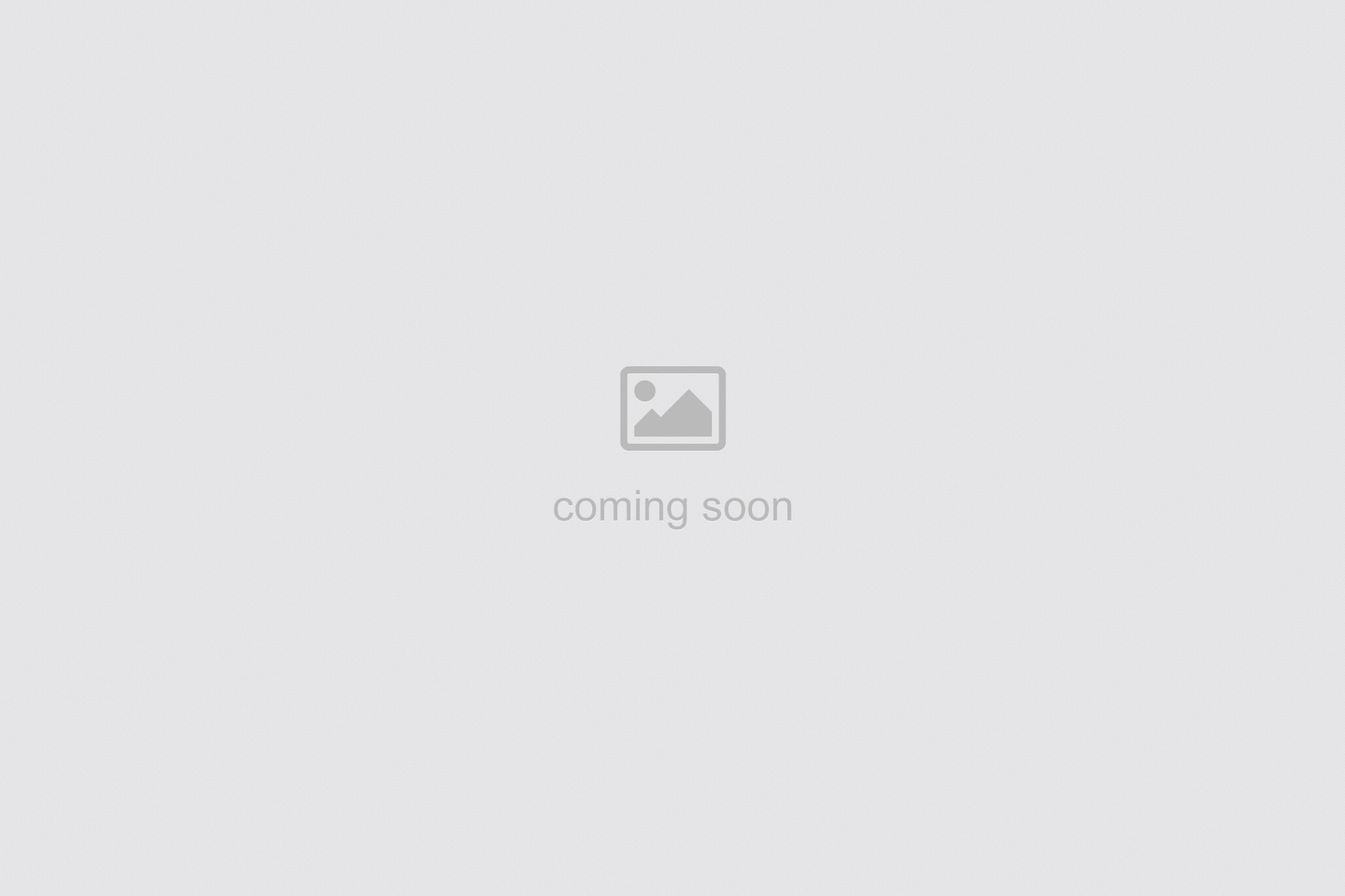
センサーアダプター&デジタル油圧計装着・SR
2023-02-06
製作しておいた「センサーアダプター」&「KOSOデジタル油圧計」の、取付にかかりました。
実際にアダプターをあてがってみると、ギリギリ収まるかと思われましたが、やはり僅かにケースやシリンダーに干渉していました。機能・強度に影響のないところでしたので、アダプターを2箇所ほど現物合わせで削り、取付可能な状態にしました。
また、アダプターのホールプラグボルト(加工穴の栓)を「イモネジ=埋め込み」にすれば、エンジン側は加工しなくても良い状態でしたが、テストや追加工の際に脱着を容易にしようと、頭の出る「キャップボルトM6」にしたため、シリンダーフィンを一部削ることにしました。
まずは、この状態で機能テスト(オイル循環・漏れ・油圧計測)しておこうと、油圧センサー・ホールプラグボルトの取付・配管を施してエンジンに装着しておきました。心配していた、油圧センサーの締め代(ネジ嵌合長)でしたが、なんとか最低限は入ったようでしっかり締めることが出来ました。その後は、メーター本体の設置(トップブリッジ上)と電源配線の加工をして一旦取付作業を完了させテストに望みました。
テストは順調で、シリンダーヘッド(ロッカーアームシャフト)側への送油が出来ている様子であり、オイル漏れは無く、油圧表示も出来ていました。とりあえず一安心の結果が得られました。
機能に問題はないことが判ったところで、取付に当たって気になった事や改良点の、追加工にとりかかることにしました。追加工したのは、次の3点です。
1点目に、やはりアダプターの取付がオイルボルト(M8)1本では不足(強度・振動による緩み)だと思われるので、1箇所支えを加えることにしました。シリンダー取付ボルト(M6)を利用(共締め)して、ステンレス板(2mm厚)で作った補助ステーを、アダプター右側にM6ボルトで取付るように追加しました。
2点目に、仮組時にバンジョウ部が供回りして、なかなか締め付けが出来なかったため、デリバリーバイプ(オイルホース)のバンジョウ部を当てるストッパーを設置しました。スペース的にかなり際どい箇所でのネジ穴加工でしたが、ホース長には余裕があったので、若干向きを変える位置でのストッパーの取付に成功しました。
最後に、送油は出来ていたものの、より流れを良くするように、オイルボルト穴の内周に溝加工を施しました。元は、ボルト穴のクリアランスを少し大き目にしてオイルが通るようにしてはいたものの、より確実に流れるように溝状(バンジョウ内側を参考)に削っておきました。
これらの追加工で、作業性が上がるとともに、確実な締め付けが出来るようになって完成させました。
肝心の油圧ですが、アイドリング時=0.4kg/cm²・約3000rpm時=0.9kg/cm²(油温23℃位)と検出(画像参照)していました。サービスマニュアルには、フィード側ポンプの標準油圧が0.8kg/cm²(アイドリング回転・油温不明記)となっていましたから、この検出箇所(クランクシャフト系と分岐した後)では、すでに圧力が低下しているということでしょう。※現状の潤滑系が正常である前提です。
ちなみに、エンジン始動直後では、1.4~1.5kg/cm²(油温10℃弱/アイドリング回転)を示していましたから、やはり油温の変化(粘度変化)による油圧への影響はかなり大きいようです。本格的に走り出す頃(春=エンジン温度などが最も安定している時期)に、基準となるデータを取りたいと思います。
※各種のデジタルメーターをどんどん追加していたら、トップブリッジが埋まってきたので、いずれはきちんとレイアウトしたメーター周りにしようと考えています。
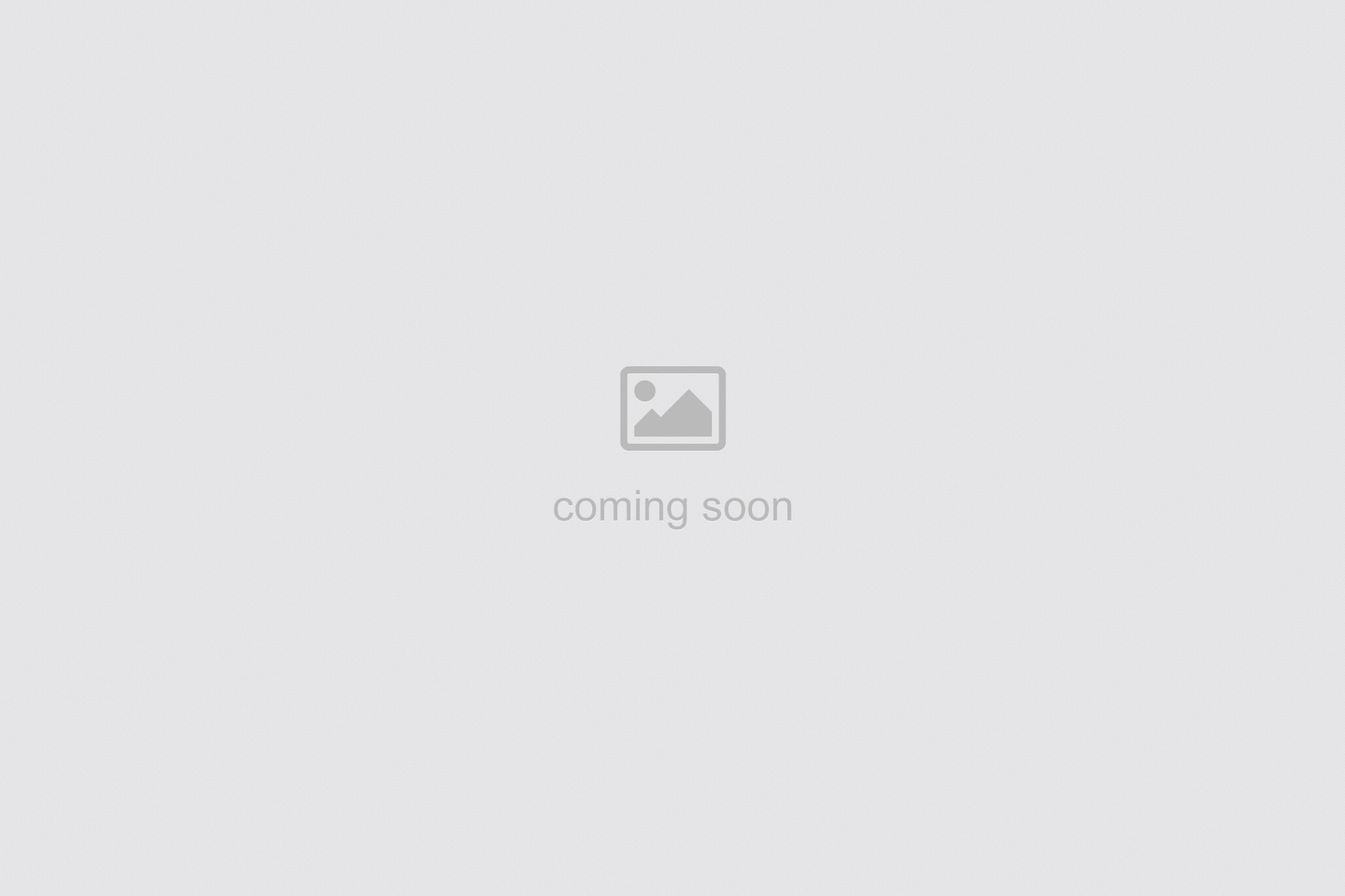